Single Pair Ethernet
Single Pair Ethernet (SPE) is a breakthrough in network technology that eliminates complexity and reduces Ethernet communication to a single twisted pair of cables. This innovation is anything but trivial: it promises to revolutionize industries where minimalist cabling is essential.
Find out how SPE is currently being used and what opportunities this technology can offer you.
The most important things at a glance:
- Ethernet speeds with only two wires
- reduces installation cost, weight, and energy consumption
- well-suited for industrial automation, automotive systems, and IoT
- can deliver data transmission speeds up to 10 Mbps over distances as long as 1,000 meters, or faster rates, such as 1 Gbps, over shorter distances, up to 40 meters
- support for Power over Data Line (PoDL)
Contents:
> What is Single Pair Ethernet?
> What Topologies are supported?
> What performance does SPE provide?
> What is the distance versus data speed trade-off for SPE?
> What are the advantages of SPE?
> What standards is SPE based on?
> Which applications is SPE used in?
> What are the advantages of using SPE in these applications?
What is Single Pair Ethernet?
Single Pair Ethernet (SPE) is a breakthrough in networking technology that strips away complexity, distilling Ethernet communication down to a single twisted pair of wires. This innovation is far from trivial: it promises to revolutionize industries where minimalism in wiring is essential—think smart factories, automobiles, and the sprawling Internet of Things (IoT). By delivering Ethernet speeds with only two wires, SPE reduces cost, weight, and energy consumption, while extending the reach of networks into places previously inaccessible to conventional Ethernet. More than just a streamlined solution, SPE represents a convergence of efficiency and capability, offering a glimpse into a future where seamless, low-cost connectivity becomes ubiquitous across all levels of modern infrastructure.
What Topologies are supported?
What performance does Single Pair Ethernet provide?
What is the distance versus data speed trade-off for Single Pair Ethernet?
Single Pair Ethernet now makes it possible to transport data at 10Mbps, 100Mbps and 1Gbps via two-wire copper cable and simultaneously supply end devices with power via Power over Data Line (PoDL).
The 10BaseT1L standard, with its "L" denoting "long-range," represents the extended-reach variant of single-pair Ethernet as defined in IEEE 802.3cg. It allows Ethernet communication over distances of up to 1000 meters on a single twisted-pair cable. Operating in full duplex mode, 10BaseT1L transmits and receives data simultaneously over a single wire pair. This is made possible through echo cancellation, a technique that subtracts the device's own outgoing signal from the incoming signal, effectively isolating the data being received. The system uses a bandwidth of 20 MHz and cables with a 100-ohm impedance, which are common in industrial environments.
Ethernet APL (Advanced Physical Layer) takes 10BaseT1L and enhances it for the unique demands of the process industry, particularly in hazardous environments. Like 10BaseT1L, it is built on the IEEE 802.3cg standard but extends the infrastructure with a "trunk-and-spur" topology suited for long cable runs. Trunk cables can stretch up to 1000 meters between field switches in Zone 1 areas, while spur cables between a switch and a device in Zone 0 can reach up to 200 meters. Additionally, Ethernet APL incorporates safety measures, like intrinsic safety (IEC TS 60079-47), and includes port profiles that allow field devices to receive power directly through the Ethernet connection—crucial for simplifying the deployment of industrial systems.
Meanwhile, 10BaseT1S, the "S" standing for "short-range," is another single-pair Ethernet variant from IEEE 802.3cg, designed for shorter distances. Unlike the long-range version, 10BaseT1S operates in half-duplex mode and supports both point-to-point and multidrop configurations. In a multidrop setup, a bus of up to 25 meters can accommodate multiple devices, each connected via spur lines of 10 centimeters in length. A switch is unnecessary, as the PLCA (Physical Layer Collision Avoidance) mechanism efficiently handles data traffic, preventing collisions and ensuring orderly communication. The standard specifies a minimum of eight spur lines, but the system can support far more, allowing for versatile network designs.
What are the advantages of Single Pair Ethernet?
A major advantage of Single Pair Ethernet is the reduction in cabling costs. As only one pair of wires is required, installation costs can be reduced and cabling simplified. This is particularly advantageous in large industrial plants or in scenarios where many devices need to be connected over long distances.
Another advantage of SPE is its support for Power over Data Line (PoDL). This allows power and data to be transmitted over the same cable, eliminating the need for additional power cables and connections. This feature is particularly useful in industrial environments where devices often need to be powered directly without installing separate power supply lines.
SPE also offers an impressive range of up to 1,000 metres, making it suitable for connecting devices over longer distances in industrial networks or long-range IoT applications. The technology is also robust and optimised for use in harsh environments where physical conditions play an important role.
The data transfer rates of Single Pair Ethernet typically reach up to 1 gigabit per second (Gbps), which is sufficient for many industrial applications and IoT scenarios. These speeds, combined with the ease of cabling and the ability to transmit power, make SPE a flexible and future-proof solution.
What standards is Single Pair Ethernet based on?
SPE spans several layers of the OSI model, particularly focusing on the Physical (Layer 1) and Data Link (Layer 2) layers. At the Physical Layer, SPE handles the electrical and mechanical characteristics of transmitting data over a single twisted pair of wires, defining how bits are encoded and sent through the cable. At the Data Link Layer, SPE defines how devices on a network exchange frames, ensuring reliable communication through error detection and flow control. The core standards that define SPE are outlined in the IEEE 802.3 family, specifically in clauses such as 802.3cg for 10 Mbps speeds and 802.3bw for 100 Mbps, with ongoing developments for higher speeds like 802.3bp and 802.3ch. These standards are based on the broader Ethernet family, following the same foundational principles of MAC addressing and frame-based communication, but optimized for environments that demand longer distances, smaller form factors, and power delivery over data lines. In short, SPE extends the well-established Ethernet paradigm to new contexts, while adhering to the same rigorous, universally recognized standards.
Traditional Fieldbus Standards and Organisations
Fieldbus communication networks, commonly used in control cabinets and power distribution boards, have been shaped by several key standards and organizations. Among these is CAN (Controller Area Network), a robust network protocol originally designed for automotive systems. CAN operates on a single, terminated twisted-pair cable and supports a multi-master architecture. It’s known for its reliability, with strong error-checking mechanisms, and offers data rates of up to 1 Mbit/sec over distances of 40 meters. When slower data rates are acceptable, such as 5 Kbit/sec, CAN can extend up to 10 kilometers. Though its data rate typically peaks at 40 KBytes/sec, CAN ensures rapid message delivery, with high-priority signals transmitted in less than 120 microseconds at 1 Mbit/sec, making it ideal for time-sensitive applications.
PROFIBUS (Process Field Bus), introduced in 1989, stands as another foundational standard for fieldbus communication, particularly in automation technology. It comes in two primary variants: PROFIBUS DP, the more widely used version for general automation tasks, and PROFIBUS PA, which is specialized for process automation. Both versions enable real-time communication across a range of devices in industrial environments, ensuring efficient data exchange within complex systems.
RS-485, or TIA-485, is another longstanding standard in the world of serial communication. It defines the electrical characteristics of drivers and receivers but does not specify higher-level protocols. RS-485 cables typically use three wires for half-duplex operation or five for full-duplex, allowing for multi-drop configurations like Ethernet, though without the ability to deliver power over the same data lines. Despite its long range, comparable to the reach of 10Base-T1L, RS-485 suffers from several limitations. It lacks support for IP protocols and cyber security, and its data throughput is significantly lower than modern alternatives. While many communication protocols—such as ModBus-serial and PROFIBUS—still use RS-485 as their physical layer, the technology, though mature and widely used, is increasingly viewed as outdated due to its slower data rates and limited security features.
The Common Industrial Protocol (CIP) is a versatile communication protocol designed for industrial automation, backed by ODVA. CIP provides an extensive set of messages and services tailored to various facets of manufacturing automation—ranging from control and safety to motion, synchronization, configuration, and information sharing. One of its key strengths is enabling seamless integration of industrial systems with enterprise-level Ethernet networks and even the broader Internet, bridging the gap between factory floors and business-level IT systems.
DeviceNet, another prominent protocol in industrial automation, operates over the Controller Area Network (CAN) and employs the Common Industrial Protocol (CIP) for communication. It defines an application layer that supports a variety of device profiles, making it suitable for applications such as data exchange, safety devices, and large I/O control systems. DeviceNet’s focus on interoperability between control devices allows for efficient and reliable communication in complex automation environments.
The HART (Highway Addressable Remote Transducer) protocol is a widely adopted communication standard that cleverly integrates digital communication into legacy 4–20 mA analog systems. Using the same pair of wires, HART transmits data at 1200 bits per second in both point-to-point and multi-drop modes. This makes it an effective solution for retrofitting older analog systems with modern digital communication without needing extensive rewiring—an appealing feature for many industrial applications.
Ethernet Standards and Organisations
Ethernet communication networks in industrial applications are governed by several key standards and organizations, each playing a crucial role in ensuring seamless data transmission and control. One of the most fundamental is IEEE 802.3, a working group within the Institute of Electrical and Electronics Engineers that defines the standards for Ethernet’s physical (PHY) and data link layers, including the all-important MAC address. In February 2019, the group released specifications for 10BASE-T1S and 10BASE-T1L under the IEEE 802.3cg standard, setting the groundwork for single-pair Ethernet in both short- and long-range applications. Currently, the group is expanding its work with 10BASE-T1M, which aims to enable longer reach and power delivery in multi-drop configurations, and is being developed under IEEE P802.3da.
The Advanced Physical Layer (APL) builds on these Ethernet standards to address the specific needs of process automation and hazardous environments. Based on IEEE and IEC standards, Ethernet-APL uses single-pair Ethernet (10BASE-T1L) but adds additional definitions that tailor the physical layer to the rigorous demands of process industries. This allows for robust two-wire Ethernet connectivity in settings where safety and reliability are paramount.
Another key standard is OPC-UA (Open Platform Communication – Unified Architecture), developed by the OPC Foundation. OPC-UA provides a comprehensive framework for information exchange across industrial automation systems. It establishes an Addressing and Information Model that supports a wide range of applications, including data access, alarm management, and service invocation, all layered over multiple transport protocols. This makes OPC-UA a powerful tool for unifying and streamlining communication across diverse industrial systems.
ODVA (Open DeviceNet Vendors Association) is a standards development organization and membership association made up of leading companies in industrial automation. Its mission is to advance open, interoperable communication technologies for the industrial sector. Since 2019, ODVA has shared its intellectual property related to the non-IEEE single-pair Ethernet (SPE) in-cabinet solution, offering users detailed insights into its benefits and impact. This effort underscores ODVA's commitment to fostering technological collaboration and innovation.
PROFINET International (PI) serves as another major force in the industrial communication landscape. As a global industry association, PI focuses on standardizing and promoting communication and information technologies for industrial automation. PI has played a pivotal role in standardizing Advanced Physical Layer (APL) technology and is actively involved in shaping SPE as an open, interoperable standard that supports seamless communication in industrial settings.
PROFINET, an industrial communication standard often written as PROFINET (Process Field Network), is specifically designed for transmitting data over Industrial Ethernet. Its strength lies in its ability to manage real-time data exchange with tight time constraints, making it indispensable for controlling and monitoring equipment in complex industrial systems.
The Open Alliance is a special interest group (SIG) that brings together automotive industry leaders and technology providers to champion Ethernet-based communication as the standard for automotive networking. The group complements existing standards like those from IEEE by providing PHY specifications tailored to the unique needs of the automotive sector, helping drive the adoption of Ethernet as a key communication backbone in vehicles.
The IEC 60603-7 standard defines the widely used RJ45 connector, originally developed for telephone systems but now the cornerstone of wired Ethernet networks. The RJ45 connector, as detailed in both the TIA-968 and IEC 60603-7 standards, specifies the connector’s physical dimensions and wiring sequences, ensuring consistent and reliable connections in local area networks (LANs).
The IEC 61850 series provides a comprehensive framework for standardizing communication networks and data models in electrical substations. A key feature of this standard is the Substation Configuration description Language (SCL), an XML-based language that allows for vendor-independent descriptions of devices and their configurations, streamlining the integration of substation equipment across different manufacturers.
Which applications is Single Pair Ethernet used in?
Single Pair Ethernet (SPE) is an emerging technology that addresses the growing demand for seamless, efficient data transmission in industries characterized by decentralized, interconnected systems. SPE is revolutionizing sectors such as automotive, industrial automation, and building infrastructure by simplifying network architectures. In automotive manufacturing, for instance, SPE is increasingly used to connect sensors, cameras, and controllers within vehicles, enabling advanced driver-assistance systems (ADAS) and in-vehicle infotainment systems with minimal wiring complexity. Industrial automation benefits from SPE’s ability to link sensors, actuators, and edge devices in smart factories, fostering real-time data exchange and machine-to-machine communication across large-scale operations. The technology is also making inroads into building automation, where it integrates lighting, HVAC systems, and security devices into unified, energy-efficient smart grids. SPE-enabled devices typically include compact sensors, controllers, and actuators, which require streamlined data and power transmission.
What are the advantages of using Single Pair Ethernet in these applications?
In the applications now served by Single Pair Ethernet (SPE), earlier technologies such as traditional Ethernet over multi-pair cables, fieldbus systems, and CAN (Controller Area Network) once held sway, particularly in automotive, industrial, and building automation environments. These legacy systems, while effective for their time, often suffered from limitations in data speed, complexity, and scalability. For instance, traditional Ethernet typically required four or eight wires, adding to cabling bulk and installation costs, while fieldbus and CAN networks—common in factories and vehicles—offered relatively low data rates and were siloed, making integration with modern IP-based systems cumbersome. SPE, by contrast, streamlines communication with just one pair of wires, significantly reducing the physical infrastructure required while still offering high data rates and long-distance reach.
The advantages of SPE lie in its simplicity and efficiency: it supports both data transmission and power delivery (Power over Data Line, or PoDL) on a single cable, slashing costs and complexity in installations that previously required separate wiring for power and data. Moreover, SPE brings Ethernet’s ubiquitous, standardized protocol to environments where fieldbus once dominated, enabling seamless communication from the sensor or actuator level all the way to the cloud. This results in improved scalability, greater flexibility for IoT-driven systems, and enhanced speed, which are essential for today’s smart factories, vehicles, and buildings. By unifying disparate systems and reducing wiring bulk, SPE not only cuts costs but also facilitates the transition to smarter, more interconnected environments, where real-time data exchange and system-wide control are paramount.
Market trends affecting the use of Single Pair Ethernet
Current market trends, particularly the rise of the Internet of Things (IoT), smart manufacturing, and energy-efficient infrastructure, are catalyzing the adoption of Single Pair Ethernet (SPE) as a pivotal technology. Traditionally, industrial networks relied on a patchwork of proprietary fieldbus systems—adequate for basic communication between sensors and controllers but insufficient for the data-rich, real-time demands of today’s interconnected devices. As industries move toward fully digitized ecosystems, where every sensor, machine, and actuator is networked for seamless data exchange, the limitations of older communication protocols have become glaring. Enter Single Pair Ethernet, a streamlined solution that delivers Ethernet's full networking power—high-speed, IP-based communication—over a single pair of copper wires, dramatically reducing both cost and complexity.
What sets SPE apart is its ability to transmit both data and power (via Power over Data Line, or PoDL) over long distances, making it ideal for industries like automotive, smart buildings, and factory automation, where space, weight, and power constraints are critical. As trends favoring lightweight, scalable, and energy-efficient technologies gain traction, SPE’s simplicity and versatility make it a natural fit for environments where traditional Ethernet infrastructure would be too cumbersome. SPE’s capacity to extend Ethernet’s universality into every corner of industrial systems—while reducing cabling bulk and enhancing energy efficiency—aligns perfectly with the broader push for more integrated, smarter, and sustainable technologies. In a world increasingly driven by data, SPE is poised to connect the smallest, most remote devices with the larger digital infrastructure, transforming how industries function in the process.
Our products
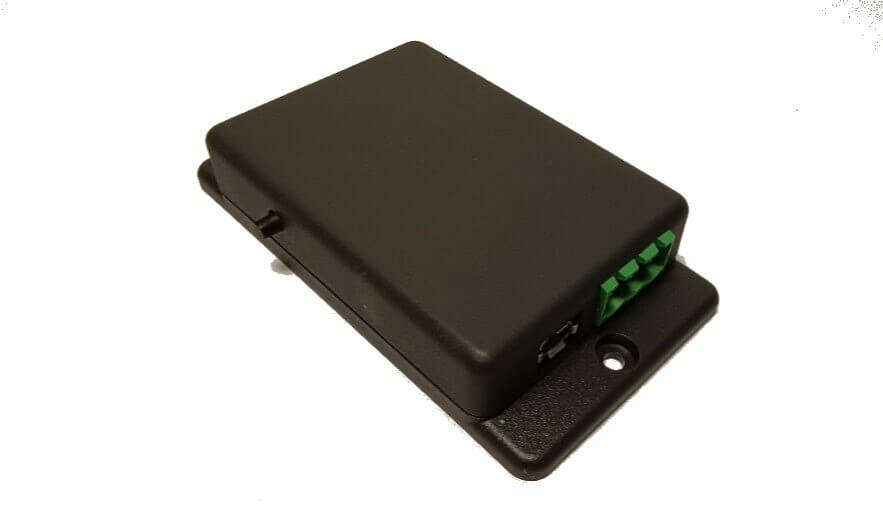
RS485 to SPE media converter
compact industrial 1-port device server
The RS485 to Single Pair Ethernet (SPE) converter supports the IEEE 802.3cg, 10BASE-T1S standards and enables the connection of RS485 devices to SPE networks, suitable for industrial environments.
Features:
- Support for various RS485 protocols: Including UART, Modbus and other protocols with separate hardware components
- Local configuration: Enables local configuration and settings
- Configurable termination for RS485: Supports configurable bus terminations
- Fail-safe logic: Prevents faulty data transmission when inputs are open on the RS485 side.
- Microchip circuits: Based on Microchip circuits compatible with IEEE 802.3cg, 10BASE-T1S and Microchip processors.
- Multiple data transmission modes:
- Transparent mode: transparent transmission between RS485 and IP/TCP/TELNET.
- Sniffer mode: Transparent transmission from RS485 RX-only to IP/TCP or IP/UDP.
- Protocol mode: The converter only responds to configured RS485 bus addresses.
- Connection of up to 32 devices
- Multihost access enables multiple hosts/servers to share serial interfaces.
- Support for token bus.
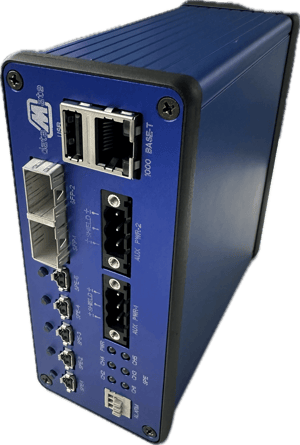
DM882x Managed SPE Switch
Family of managed switches for our customer dataMate
The DM882x is a family of managed switches for Single Pair Ethernet deployed for TSN. The DM882x is supported by mainline Linux and has no proprietary management stack, which can be freely customized by the customer to meet their specific application requirements.
Features:
- Managed switch with 5 SPE ports and 2 uplink ports
- Based on ADIN6310 Industrial Ethernet TSN switch with integrated security
- SCCP negotiated SPoE performance up to class 14 per SPE Chanel with FAULT protection
- Variants for IEC 63171-x and Terminal Block SPE connectors
- 24V/48V AUX input power with redundant input input
- Line interface 1.5kV electrical isolation & K.21 lightning protection
- Supported in Mainline Linux